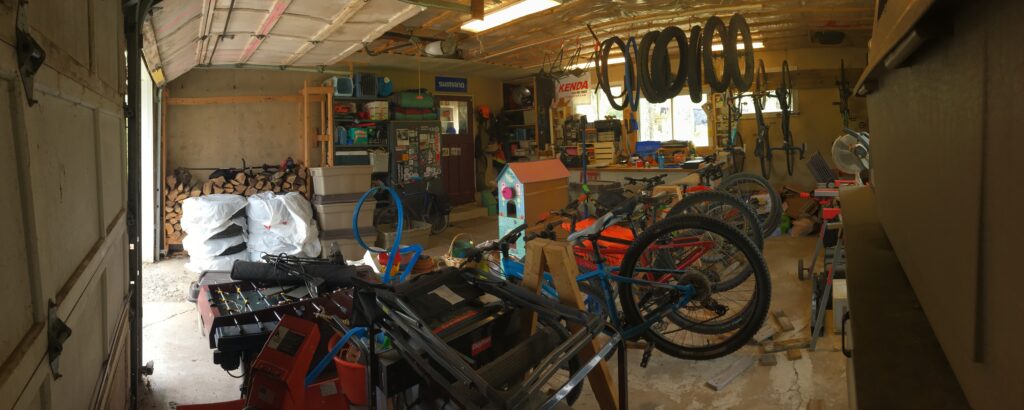
That time when everything has to be moved around to accommodate the coming and passing season. There are generally only two of these each year, one in Fall to Winter and one in Spring to Summer.
I have a two car garage that has only ever had one car in it. Lyn gets to keep her car in it in the winter time so she doesn’t have to clean it off. The other 3 seasons it’s left to bikes and other stuff. The garage primarily holds stuff relevant to the current season. The Garage is Central Processing.

The changeover is slow. It can sometimes take a period of several weeks, worked on in chunks of hours at a time here and there, hence the state of disarray. I generally try and get it done as quickly and cleanly as possible.
Currently Central Processing is filled with stuff on it’s way out. Winter tires for the cars that have been removed. The Snowblower. Some bags of salt/ice melt. These will be transported to Storage and Waste Management. There are also other items to be processed. Bins of Lyn’s plant pots and potting materials that need to be established in some new location. A dollhouse, foosball table, miscellaneous toys, a drill press and random Thule rack pieces that need to be re-homed. The backlog is growing.
Non-relevant seasonal items need to be moved from Central Processing to Storage and Waste Management. This is often done with the aid of a re-puposed Radio Flyer wagon. Storage and Waste Management is a ‘shed’ at the rear of The Fack Ranch property where items are either stored during their respective ‘off’ season or sorted and distributed either to be trashed/taken to the dump, recycled, or burned.

Currently, Storage and Waste Management has quite a few items to be rotated to Central Processing. The lawn mower. All the garden hand tools. The steps that go into the pool (also as yet to be opened for the season) and various pool accessories.
Storage and Waste Management – as it’s name implies – also permanently stores many things. The lean-to next to it covers my main stockpile of firewood that feeds the smaller stockpile I keep in the garage. Inside the barn is my ‘collection’ of far too much ‘reclaimed’ wood. Leftovers from various projects that may be of use some day, miscellaneous pieces retrieved when disassembling various items/structures, etc. Some of it, if too warped, bent or rotten simply gets burned, but if it’s moderately useable it will be kept, at least temporarily.

Other items currently in storage are a non-functional 4-wheeler that I partially disassembled in hopes of ‘restoring’ but then realized I was in over my head. When it comes to small engines, I am a cyclist. It’s future remains a mystery. There’s a small garden trailer. There’s several items that were put here for ‘later use’, but now have languished so long that they are no longer salvageable and are now considered ‘waste’. These include remnants of flooring, several old baseboard heaters and some random light fixtures as well as an old shower enclosure (don’t ask).
The one drawback of Storage and Waste Management is that it is not – ahem – ‘weather tight’. It sits on an old (failing) fieldstone foundation and as such there is a great deal of daylight in spots at the base of the structure as well as points throughout. In other words, it’s a wildlife habitat. Often times the best intentions of saving something for later use are foiled by something deciding it makes great nesting material. Oh well. Them’s the breaks. ‘Country Living’ I believe it’s called.
There is a second story to Storage and Waste Management, but it’s only accessible via a rather questionable ladder at the inside rear of the structure so not much is kept up there, as it’s difficult to get bigger/heavier stuff up top.
On the Waste Management side, this is where things go to be stockpiled for eventual removal to the landfill or recycling depot. Landfill trips usually only occur 2-3 times a year so this can sometimes mean a backlog of materials awaiting extrication, lending only further to the ‘Backcountry’ Aesthetic. (See box spring and derelict hockey goals to the right in ‘Figure 37A’)
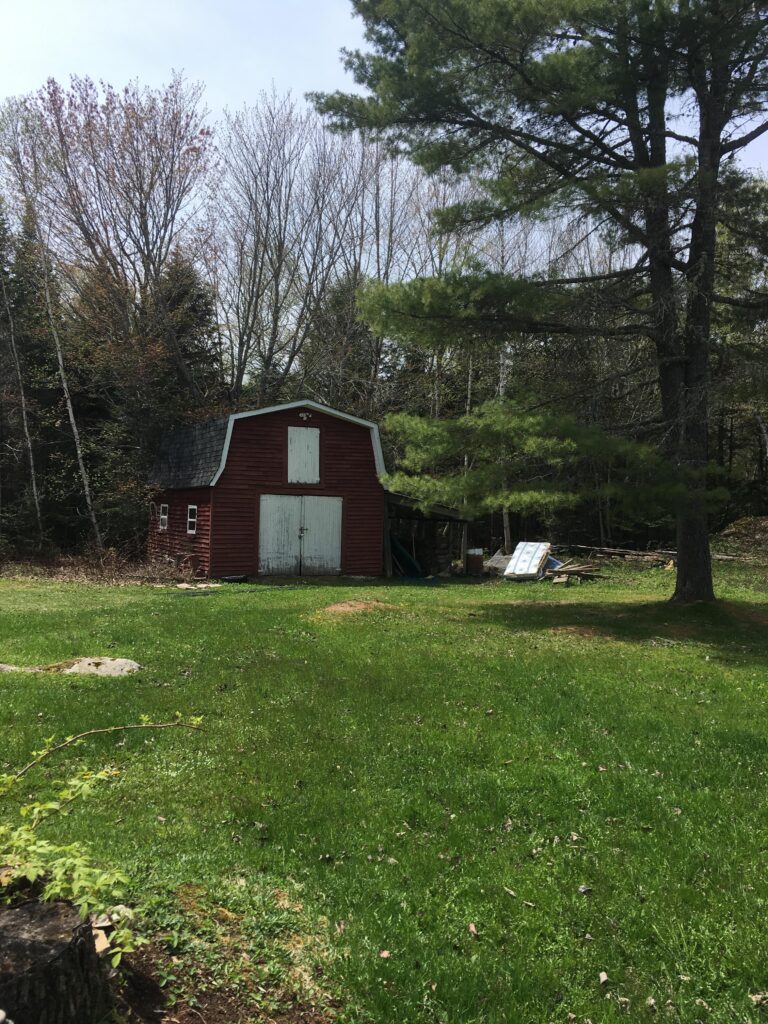
Where the Hell is Everything
Although I’m pretty fastidious with systems and labelling, in an operation of this size there is still some product loss issues. After 6 months I sometimes don’t remember where I’ve put shit. During the Seasonal Changeover there is also the process of Inventory Repair and Replacement. Often times at the end of a season, if something is broken beyond repair it is discarded and a ‘mental note’ is made to ‘replace next year’. If it’s repairable, a note is made to ‘repair next year’, so these items need to be sorted as well. Often, due to filing inaccuracies or clerical error, these mental notes get lost or filed incorrectly and this can lead to delays in the Seasonal Changeover process. In addition, Inventory is sometimes not accurate and things are indeed, not where the hell you thought they were.
One side-effect of this is often thinking when you can’t find something that it must have been broken last year, deemed ‘irreparable’ by Facilities Management and disposed of. You end up purchasing a new item, only to find the fully-functioning old item later on, which, due to an error in Inventory – usually the loss of a ‘mental note’ – had been right where you put it leading to an instance of redundancy, which is not always desirable, but often times is sorted naturally, when you get mad and break one of the redundant items, usually by trying to use it for something other than it’s intended purpose – also known as the Everything is Not Necessarily a Hammer Principle.
This year the changeover is going reasonably well. The issue of finding the component to house all Lyn’s potting/plant stuff has led to a bit of a logjam in Central Processing, but with roughly one and a half days worth of Man-hours into the process, I’m feeling pretty confident. Folly for sure, as I’ve added to the docket this year my intention to remove all that reclaimed wood I mentioned earlier, lay it out in the yard, and sort it for easier retrieval when needed. That may have to break out into a work docket all it’s own due to the complexity and time requirements of such a project. I’ll have to consult with Project Scheduling and Management on that. I anticipate a breakout workgroup session to strategize on on implementation of wood sorting best practices and optimization of metrics to determine maximum ROI.
And I’ll probably end up burning some stuff.